AEROSPACE FORGINGS
AEROSPACE FORGINGS
Forgings refer to products manufactured by the process of shaping metal utilizing compressive forces. The compressive forces used are generally delivered via pressing, pounding, or squeezing under great pressure. Although there are many different kinds of forging processes available, they can be grouped into three main classes:
Drawn out: length increases, cross-section
Upset: length decreases, cross-section increases decreases
Squeezed in closed compression dies: produces multidirectional flow
Forging produces pieces that are stronger than an equivalent cast or machined part. As the metal is shaped during the forging process, the internal grain deforms to follow the general shape of the part. This results in a grain that is continuous throughout the part, resulting in its high strength characteristics. Forgings are broadly classified as either cold, warm or hot forgings, according to the temperature at which the processing is performed. Iron and steel are nearly always hot forged, which prevents the work hardening that would result from cold forging. Work hardening increases the difficulty of performing secondary machining operations on the metal pieces. When work hardening is desired, other methods of hardening, most notably heat treating, may be applied to the piece. Alloys such as aluminum and titanium that are amenable to precipitation hardening can be hot forged, followed by hardening. Because of their high strength, forgings are almost always used where reliability and human safety are critical such as in the aerospace, automotive, ship building, oil drilling, engine and petrochemical industries.
For more information or to receive a prompt aluminum price quote, please contact us at 800 398-4345 or submit the INSTAQUOTE Form.
HIGH TEMP SUPER ALLOY FORGING
TYPE | SPECIFICATIONS |
---|---|
AERMET 100™ | AMS6532 |
A286 | AMS5731, 5731, 5737, B50T1180 |
HASTELLOY X± | AMS5754, B50TF31 |
HAYNES 188± | MS5772, B50TF74 |
HAYNES 230± | AMS5891, ASTM-B564 |
HAYNES 25± (L605) | AMS5759 |
INCONEL 600* | AMS5665, ASTM-B564 |
INCONEL 625* | AMS5666, B50TF133, ASTB-B564 |
INCONEL 718* | AMS5662, 5663, 5664, B50TF15, C50TF103 |
INCONEL X-750* | AMS5667, 5668, 5670, 5671, 5747, B50T1232 |
MONEL 400* | ASTM-B164, QQ-N-281 |
MONEL K500* | AMS4676, QQ-N-286, ASTM-B564 |
RENE 41* | AMS5712, 5713, B50TF75, B50TF110 |
WASPALOY• | AMS5704, 5706, 5707, 5708, 5709 |
• Trademark United Technologies
* Trademark Inco Alloys
± Trademark Haynes International
™ Trademark Trademark Carpenter
TITANIUM FORGING
TYPE | SPECIFICATIONS |
---|---|
CP-GRADES 1, 2, 3, 4 | AMS4921, ASTM-B348 |
6Al-4V | AMS4928, 4931, 4965, AMS-T-9047, C50TF12 |
6Al-4V ELI | AMS4930, 4931, 6932, BMS-7-269 |
6Al-2Sn-4Zr-2Mo | AMS495, 4976, B50TF22 |
6Al-6V-2Sn | AMS4978 |
8Al-1Mo-1V | AMS4972, 4973, C50T81 |
10V-2Fe-3Al | AMS4983 |
ALLOY STEEL FORGING
TYPE | SPECIFICATIONS |
---|---|
4130 | AMS6370, AMS-S-6758 |
4140 | AMS6382, AMS-S-5626 |
4330 MOD | AMS6411, 6427 |
4340 | AMS6414, 6415 |
4340 MOD / 300M | AMS6257, 6417, 6419, MIL-S-8844 CL-3 |
8620 | AMS6274, 6276 |
8740 | AMS6322, AMS-S-6049 |
9310 | AMS6260, 6265 |
52100 | AMS6440, 6444 |
NITRALLOY 135 MOD | AMS6470, 6471 |
ALUMINUM FORGING
TYPE | SPECIFICATIONS |
---|---|
2014 | AMS4133, 4134, 4314, AMS-A-22771 |
2024 | AMS-QQ-A-367 |
2219 | AMS4143, 4144, AMS-QQ-A-367, AMS-A-22771 |
2618 | AMS4132, AMS-QQ-A-367, AMS-A-22771 |
6061 | AMS4127, 4146, AMS-QQ-A-367, AMS-A-22771 |
7049 | AMS4111, AMS-QQ-A-367, AMS-A-22771 |
7050 | AMS4107, 4108, AMS-A-22771 |
7075 | AMS4126, 4131, 4141, 4147, AMS-QQ-A-367 |
7079 | AMS-QQ-A-367 |
7150 | AMS-A-22771 |
7175 | AMS4148, 4149, 4179, AMS-A-22771 |
stainless steel forging
TYPE | SPECIFICATIONS |
---|---|
PH13-8MO | AMS5629 |
15-5PH | AMS5659 |
15-7PH | AMS5657 |
17-4PH | AMS5643 |
17-7PH | AMS5644 |
AM-355 | AMS5743 |
CUSTOM 455 | AMS5617 |
304, 304L | AMS5639 |
304, 304L | AMS5653 |
321 | AMS5645 |
347 | AMS5646 |
410 | AMS5613 |
416 | AMS5610 |
418 (GREEK ASCOLOY) | AMS5616 |
420 | AMS5620 |
430 | AMS5627 |
431 | AMS5628 |
440A | AMS5631 |
440C | AMS5630 |
NITRONIC 40 | AMS5656 |
NITRONIC 50 | AMS5764 |
NITRONIC 60 | AMS5848 |
ON-TIME DELIVERY
OPEN DIE FORGING
Open die forging is performed between flat dies with no precut profiles in the dies. Movement of the workpiece is the key to this method. Larger parts over 200,000 lbs. and 80 feet in length can be hammered or pressed into shape this way.
Open-die forging can produce forgings from a few pounds up to more than 150 tons. Called open-die because the metal is not confined laterally by impression dies during forging, this process progressively works the starting stock into the desired shape, most commonly between flat-faced dies. In practice, open-die forging comprises many process variations, permitting an extremely broad range of shapes and sizes to be produced. In fact, when design criteria dictate optimum structural integrity for a huge metal component, the sheer size capability of open-die forging makes it the clear process choice over non-forging alternatives. At the high end of the size range, open-die forgings are limited only by the size of the starting stock, namely, the largest ingot that can be cast. Practically all forgeable ferrous and non-ferrous alloys can be open-die forged, including some exotic materials like age-hardening superalloys and corrosion-resistant refractory alloys.
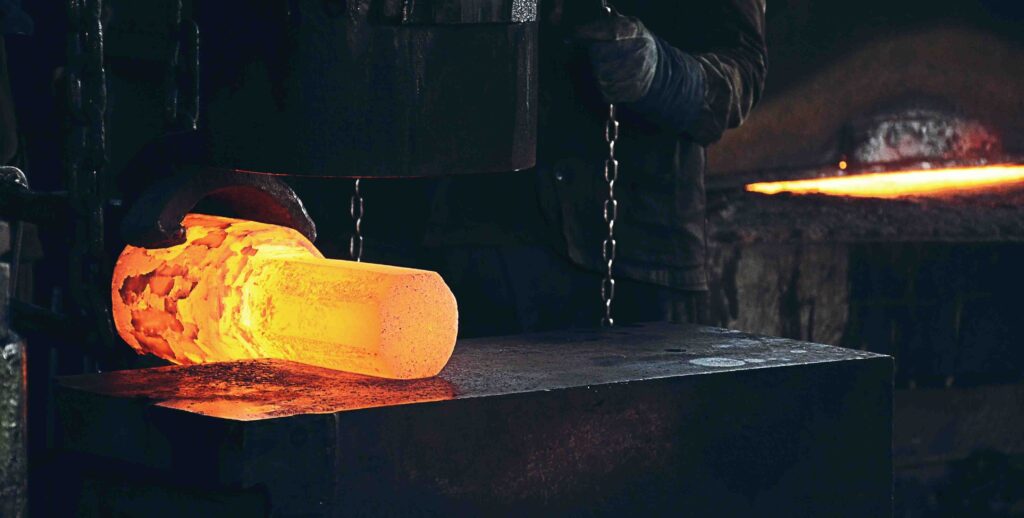
SEAMLESS ROLLED RING FORGING
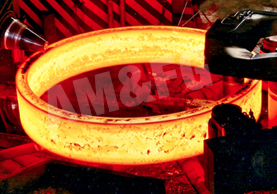
Seamless rolled ring forging is typically performed by punching a hole in a thick, round piece of metal (creating a donut shape), and then rolling and squeezing (or in some cases, pounding) the donut into a thin ring. Ring diameters can be anywhere from a few inches to 30 feet. Rings forged by the seamless ring rolling process can weigh < 1 lb up to 350,000 lbs., while O.D.’s range from just a few inches up to 30-ft. in diameter. Performance-wise, there is no equal for forged, circular-cross-section rings used in energy generation, mining, aerospace, off-highway equipment and other critical applications.
High tangential strength and ductility make forged rings well-suited for torque- and pressure-resistant components, such as gears, engine bearings for aircraft, wheel bearings, couplings, rotor spacers, sealed discs and cases, flanges, pressure vessels and valve bodies. Materials include not only carbon and alloy steels, but also non-ferrous alloys of aluminum, copper and titanium, as well as nickel-base superalloys.
TECHNICAL DATA SHEETS
- Aluminum 2014A Composition Spec
- Aluminum 2024A Composition Spec
- Aluminum 2618A Composition Spec
- Aluminum 6061A Composition Spec
- Aluminum 7049A Composition Spec
- Aluminum 7050A Composition Spec
- Aluminum 7150 Composition Spec
- Titanium Ti-6Al-2Sn-4Zr-2Mo-0.1Si; Duplex Annealed
- Carpenter AerMet 100, 900°F Aged
- Carpenter AerMet 100, 875°F Aged
- Haynes® 230® alloy, as cast vacuum investment casting, tested at RT
- Haynes® 230® alloy, as cast vacuum investment casting, tested at 538°C (1000°F)
- Haynes® 230® alloy, as cast vacuum investment casting, tested at 649°C (1200°F)
- Haynes® 230® alloy, as cast vacuum investment casting, tested at 760°C (1400°F)
- Haynes® 230® alloy, as cast vacuum investment casting, tested at 871°C (1600°F)
- Haynes® 230® alloy, as cast vacuum investment casting, tested at 982°C
- Haynes® 230® alloy, as cast vacuum investment casting, tested at 1093°C
- Haynes® 25 alloy, vacuum investment castings, solution treated, tested at RT
- Haynes® 25 alloy, vacuum investment castings, solution treated, tested at 425°C (800°F)
- Haynes® 25 alloy, vacuum investment castings, solution treated, tested at 650°C (1200°F)
- Haynes® 25 alloy, vacuum investment castings, solution treated, tested at 760°C (1400°F)
- Haynes® 25 alloy, vacuum investment castings, solution treated, tested at 870°C (1600°F)
- Haynes® 25 alloy, vacuum investment castings, solution treated, tested at 980°C (1800°F)
- Special Metals MONEL™ Alloy 400
- Special Metals MONEL™ Alloy K-500
- Allegheny Ludlum Grade 1 Titanium (UNS R50250)
- Allegheny Ludlum Grade 2 Titanium (UNS R50400)
- Allegheny Ludlum Grade 3 Titanium (UNS R50550)
- Allegheny Ludlum Grade 4 Titanium (UNS R50700)
- Allegheny Ludlum Titanium 6Al-4V ELI (UNS R56401)
- MetalTek WASPALOY® Centri-Vac Nickel Cobalt Based Alloy
- TIMETAL® 10-2-3 Titanium Alloy (Ti-10V-2Fe-3Al), Aged Billet/Bar per ASTM 4984
- TIMETAL® 10-2-3 Titanium Alloy (Ti-10V-2Fe-3Al), Aged Billet/Bar per ASTM 4986
- TIMETAL® 10-2-3 Titanium Alloy (Ti-10V-2Fe-3Al), Aged Billet/Bar per ASTM 4987
- TIMETAL® 35A CP Titanium (ASTM Grade 1)
- TIMETAL® 50A CP Titanium (ASTM Grade 2)
- TIMETAL® 6-2-4-6 Titanium Alloy (Ti-6Al-2Sn-4Zr-6Mo), Beta Forged + STA
- TIMETAL® 62S Titanium Alloy (Ti-6Al-2Fe-0.1Si); Alpha-Beta Forged, RA
- TIMETAL® 62S Titanium Alloy (Ti-6Al-2Fe-0.1Si); Beta Forged
- TIMETAL® 65A CP Titanium (ASTM Grade 3)
- TIMETAL® 75A CP Titanium (ASTM Grade 4)
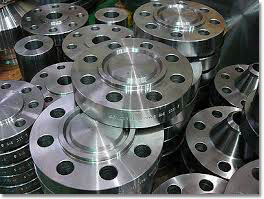
Forged parts vary in size, shape and sophistication and can be produced using nearly any metal. The most common metals used include carbon, alloy, tool and stainless steels as well as aluminum, titanium, high-temperature superalloys, brass and copper.
High strength-to-weight ratios and structural reliability favorably influence performance, range and payload capabilities in the aerospace industry. Made of ferrous, non-ferrous and special alloy materials, forgings are widely used in jets and piston-engine planes, helicopters, engine mounts, military aircraft and spacecraft. Some examples of where a forging’s versatility of size, shape and properties make it an ideal component include bulkheads, wing roots and spars, hinges, engine mounts, brackets, beams, shafts, landing gear cylinders and struts, wheels, brake carriers and discs and arresting hooks. In jet turbine engines, iron-base, nickel-base and cobalt-base superalloys are forged into components such as discs, blades, buckets, couplings, manifolds, rings, chambers and shafts.
STILL HAVE ANY QUESTIONS? IS SOMETHING UNCLEAR? DO NOT SEE WHAT YOU ARE LOOKING FOR? AEROSPACE SPECIFICATION SERVICES FRIENDLY SALES TEAM IS WAITING FOR YOUR CALL AT 800-398-4345 OR SEND US AN EMAIL