NICKEL ALLOY TECHNICAL DATA
- Allegheny Ludlum Altemp® A286 Iron-Base Superalloy, UNS S66286
- Haynes® 188 alloy, 0% cold reduction, 3.2 mm thick sheet
- Haynes® 188 alloy, 10% cold reduction, 3.2 mm thick sheet
- Haynes® 188 alloy, 10% cold reduction, 3.2 mm thick sheet, 1065°C for 5 minutes
- Haynes® 188 alloy, 10% cold reduction, 3.2 mm thick sheet, 1120°C for 5 minutes
- Haynes® 188 alloy, 10% cold reduction, 3.2 mm thick sheet, 1175°C for 5 minutes
- Haynes® 188 alloy, 20% cold reduction, 3.2 mm thick sheet
- Haynes® 188 alloy, 20% cold reduction, 3.2 mm thick sheet, 1065°C for 5 minutes
- Haynes® 188 alloy, 20% cold reduction, 3.2 mm thick sheet, 1120°C for 5 minutes
- Haynes® 188 alloy, 20% cold reduction, 3.2 mm thick sheet, 1175°C for 5 minutes
- Haynes® 188 alloy, 30% cold reduction, 3.2 mm thick sheet
- Haynes® 188 alloy, 30% cold reduction, 3.2 mm thick sheet, 1065°C for 5 minutes
- Haynes® 188 alloy, 30% cold reduction, 3.2 mm thick sheet, 1120°C for 5 minutes
- Haynes® 188 alloy, 30% cold reduction, 3.2 mm thick sheet, 1175°C for 5 minutes
- Haynes® 188 alloy, 40% cold reduction, 3.2 mm thick sheet
- Haynes® 188 alloy, 40% cold reduction, 3.2 mm thick sheet, 1065°C for 5 minutes
- Haynes® 188 alloy, 40% cold reduction, 3.2 mm thick sheet, 1120°C for 5 minutes
- Haynes® 188 alloy, 40% cold reduction, 3.2 mm thick sheet, 1175°C for 5 minutes
- Haynes® 188 alloy, cold rolled and 1175°C solution annealed sheet, tested at 1095°C (2000°F)
- Haynes® 188 alloy, cold rolled and 1175°C solution annealed sheet, tested at 540°C (1000°F)
- Haynes® 188 alloy, cold rolled and 1175°C solution annealed sheet, tested at 650°C (1200°F)
- Haynes® 188 alloy, cold rolled and 1175°C solution annealed sheet, tested at 760°C (1400°F)
- Haynes® 188 alloy, cold rolled and 1175°C solution annealed sheet, tested at 870°C (1600°F)
- Haynes® 188 alloy, cold rolled and 1175°C solution annealed sheet, tested at 980°C (1800°F)
- Haynes® 188 alloy, cold rolled and 1175°C solution annealed sheet, tested at RT
- Haynes® 188 alloy, hot rolled and 1175°C solution annealed plate, tested at 1095°C (2000°F)
- Haynes® 188 alloy, hot rolled and 1175°C solution annealed plate, tested at 1150°C (2100°F)
- Haynes® 188 alloy, hot rolled and 1175°C solution annealed plate, tested at 1205°C (2200°F)
- Haynes® 188 alloy, hot rolled and 1175°C solution annealed plate, tested at 540°C (1000°F)
- Haynes® 188 alloy, hot rolled and 1175°C solution annealed plate, tested at 650°C (1200°F)
- Haynes® 188 alloy, hot rolled and 1175°C solution annealed plate, tested at 760°C (1400°F)
- Haynes® 188 alloy, hot rolled and 1175°C solution annealed plate, tested at 870°C (1600°F)
- Haynes® 188 alloy, hot rolled and 1175°C solution annealed plate, tested at 980°C (1800°F)
- Haynes® 188 alloy, hot rolled and 1175°C solution annealed plate, tested at RT
- Haynes® 188 alloy, plate at RT after 0 hours at 650°C (1200°F)
- Haynes® 188 alloy, plate at RT after 0 hours at 760°C (1400°F)
- Haynes® 188 alloy, plate at RT after 0 hours at 870°C (1600°F)
- Haynes® 188 alloy, plate at RT after 1000 hours at 870°C (1600°F)
- Haynes® 188 alloy, plate at RT after 16000 hours at 870°C (1600°F)
- Haynes® 188 alloy, plate at RT after 4000 hours at 870°C (1600°F)
- Haynes® 188 alloy, plate at RT after 8000 hours at 650°C (1200°F)
- Haynes® 188 alloy, plate at RT after 8000 hours at 760°C (1400°F)
- Haynes® 188 alloy, plate at RT after 8000 hours at 870°C (1600°F)
- Haynes® Hastelloy® X alloy, sheet, tested at 1095°C (2000°F)
- Haynes® Hastelloy® X alloy, sheet, tested at 540°C (1000°F)
- Haynes® Hastelloy® X alloy, sheet, tested at 650°C (1200°F)
- Haynes® Hastelloy® X alloy, sheet, tested at 760°C (1400°F)
- Haynes® Hastelloy® X alloy, sheet, tested at 870°C (1600°F)
- Haynes® Hastelloy® X alloy, sheet, tested at 980°C (1800°F)
- Haynes® Hastelloy® X alloy, sheet, tested at RT
- Haynes® Multimet® alloy, 1.32 mm thick sheet, 1177°C heat treatment, rapid air cooled, tested at 1038°C
- Haynes® Multimet® alloy, 1.32 mm thick sheet, 1177°C heat treatment, rapid air cooled, tested at 649°C (1200°F)
- Haynes® Multimet® alloy, 1.32 mm thick sheet, 1177°C heat treatment, rapid air cooled, tested at 927°C
- Haynes® Multimet® alloy, 1.32 mm thick sheet, 1177°C heat treatment, rapid air cooled, tested at RT
- Haynes® Multimet® alloy, 1.6 mm thick sheet, 1177°C heat treatment, rapid air cooled, tested at 1093°C
- Haynes® Multimet® alloy, 1.6 mm thick sheet, 1177°C heat treatment, rapid air cooled, tested at 1149°C (2100°F)
- Haynes® Multimet® alloy, 1.6 mm thick sheet, 1177°C heat treatment, rapid air cooled, tested at 1204°C (2200°F)
- Haynes® Multimet® alloy, 1.6 mm thick sheet, 1177°C heat treatment, rapid air cooled, tested at 1260°C
- Haynes® Multimet® alloy, 1.6 mm thick sheet, 1177°C heat treatment, rapid air cooled, tested at 1288°C
- Haynes® Multimet® alloy, 1.6 mm thick sheet, 1177°C heat treatment, rapid air cooled, tested at 427°C (800°F)
- Haynes® Multimet® alloy, 1.6 mm thick sheet, 1177°C heat treatment, rapid air cooled, tested at 538°C (1000°F)
- Haynes® Multimet® alloy, 1.6 mm thick sheet, 1177°C heat treatment, rapid air cooled, tested at 649°C (1200°F)
- Haynes® Multimet® alloy, 1.6 mm thick sheet, 1177°C heat treatment, rapid air cooled, tested at 760°C (1400°F)
- Haynes® Multimet® alloy, 1.6 mm thick sheet, 1177°C heat treatment, rapid air cooled, tested at 871°C (1600°F)
- Haynes® Multimet® alloy, 1.6 mm thick sheet, 1177°C heat treatment, rapid air cooled, tested at 982°C
- Haynes® Multimet® alloy, 1.6 mm thick sheet, 1177°C heat treatment, rapid air cooled, tested at RT
- Haynes® Multimet® alloy, 12.7 mm (1/2 in.) thick plate, 1185°C heat treatment, water quenched, tested at -196°C
- Haynes® Multimet® alloy, 12.7 mm (1/2 in.) thick plate, 1185°C heat treatment, water quenched, tested at -78°C
- Haynes® Multimet® alloy, 12.7-50.8 mm hot-rolled bar, 1185°C heat treatment, water quenched, tested at RT
- Haynes® Multimet® alloy, 25.4-50.8 mm forged bar, 1185°C heat treatment, water quenched, tested at RT
- Haynes® Multimet® alloy, 533.4 by 82.55 mm forging, stress relieved at 649°C (1200°F), air cooled, tested at 649°C (1200°F)
- Haynes® Multimet® alloy, 533.4 by 82.55 mm forging, stress relieved at 649°C (1200°F), air cooled, tested at RT
- Haynes® Multimet® alloy, 6.15 mm hot-rolled bar, 10% cold reduction, tested at RT
- Haynes® Multimet® alloy, 6.15 mm hot-rolled bar, 1185°C heat treatment, rapid air cooled, tested at RT
- Haynes® Multimet® alloy, 6.15 mm hot-rolled bar, 15% cold reduction, tested at RT
- Haynes® Multimet® alloy, 6.15 mm hot-rolled bar, 20% cold reduction, tested at RT
- Haynes® Multimet® alloy, 6.15 mm hot-rolled bar, 25% cold reduction, tested at RT
- Haynes® Multimet® alloy, 6.15 mm hot-rolled bar, 30% cold reduction, tested at RT
- Haynes® Multimet® alloy, 6.15 mm hot-rolled bar, 35% cold reduction, tested at RT
- Haynes® Multimet® alloy, 6.15 mm hot-rolled bar, 40% cold reduction, tested at RT
- Haynes® Multimet® alloy, 6.15 mm hot-rolled bar, 5% cold reduction, tested at RT
- Haynes® Waspaloy™ alloy, sheet, tested at 1095°C (2000°F)
- Haynes® Waspaloy™ alloy, sheet, tested at 650°C (1200°F)
- Haynes® Waspaloy™ alloy, sheet, tested at 760°C (1400°F)
- Haynes® Waspaloy™ alloy, sheet, tested at 870°C (1600°F)
- Haynes® Waspaloy™ alloy, sheet, tested at 980°C (1800°F)
- Haynes® Waspaloy™ alloy, sheet, tested at RT
- Nickelvac® A-286 Specialty Steel, Heat Treatment: 982°C (1800°F) + Age
- Nickelvac® L-605 Nickel Superalloy, Heat Treatment: 1204°C (2200°F) Anneal
- Rene 41® Nickel Superalloy, Heat Treatment: 1079°C (1975°F) + Age
- Special Metals INCO® A-286 Iron-Nickel-Chromium Alloy
- Special Metals INCONEL® Alloy 600
- Special Metals INCONEL® Alloy 617
- Special Metals INCONEL® Alloy 625
- Special Metals INCONEL® Alloy 718
- Special Metals INCONEL® Alloy X-750
- Special Metals NIMONIC™ Alloy 901
- Waspaloy® Nickel Superalloy, Heat Treatment: 1010°C (1850°F) + Age
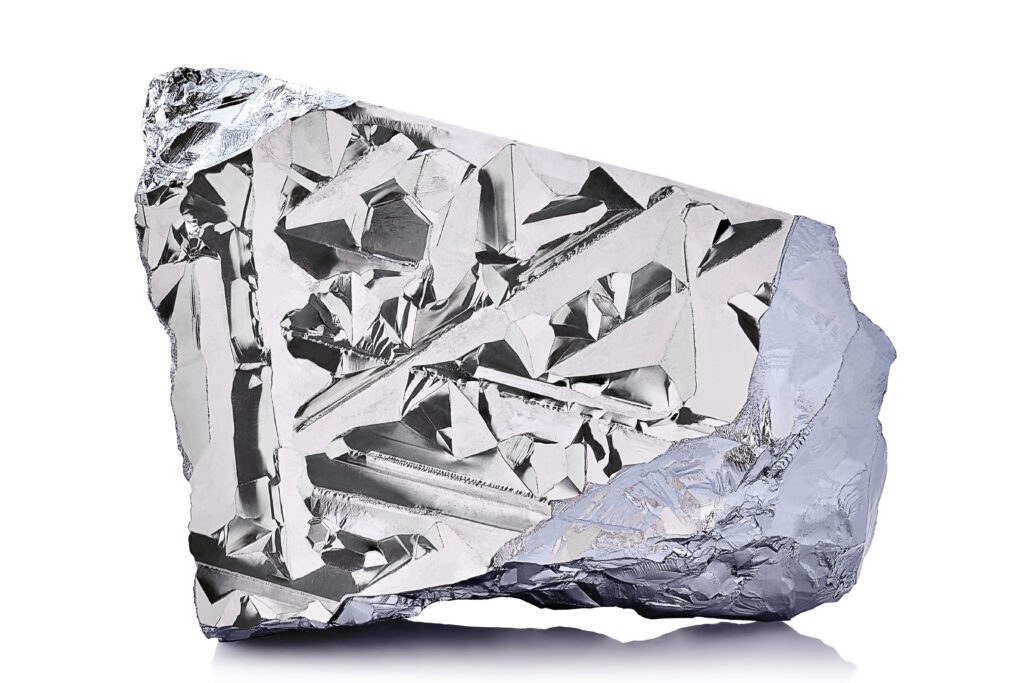
Nickel-based Superalloys have been developed for very high temperature applications where relatively high stresses are encountered and where high surface stability is frequently required. Nickel is a very versatile metal with many applications in the aerospace industry. It’s ability to alloy with a wide range of metals has brought it to the forefront of metallurgy. Nickel alloys possess high strength and excellent corrosion resistance, particularly in aerospace applications where elevated temperatures are present. Cobalt is a strategic and critical metal used in many diverse commercial, industrial, and military applications. The largest use of cobalt in the aerospace industry is to make parts for gas turbine aircraft engines. Heat resistant alloys of nickel and cobalt are used where high temperature performance, particularly creep resistance, is required. These alloys have been typically selected for gas turbine components such as blades, turbine wheels and latter stage compressor disks, which are subjected to long term rotational stresses and high temperatures.